Efficient Manufacturing & Material Handling
Your Production Goals. Our Execution.
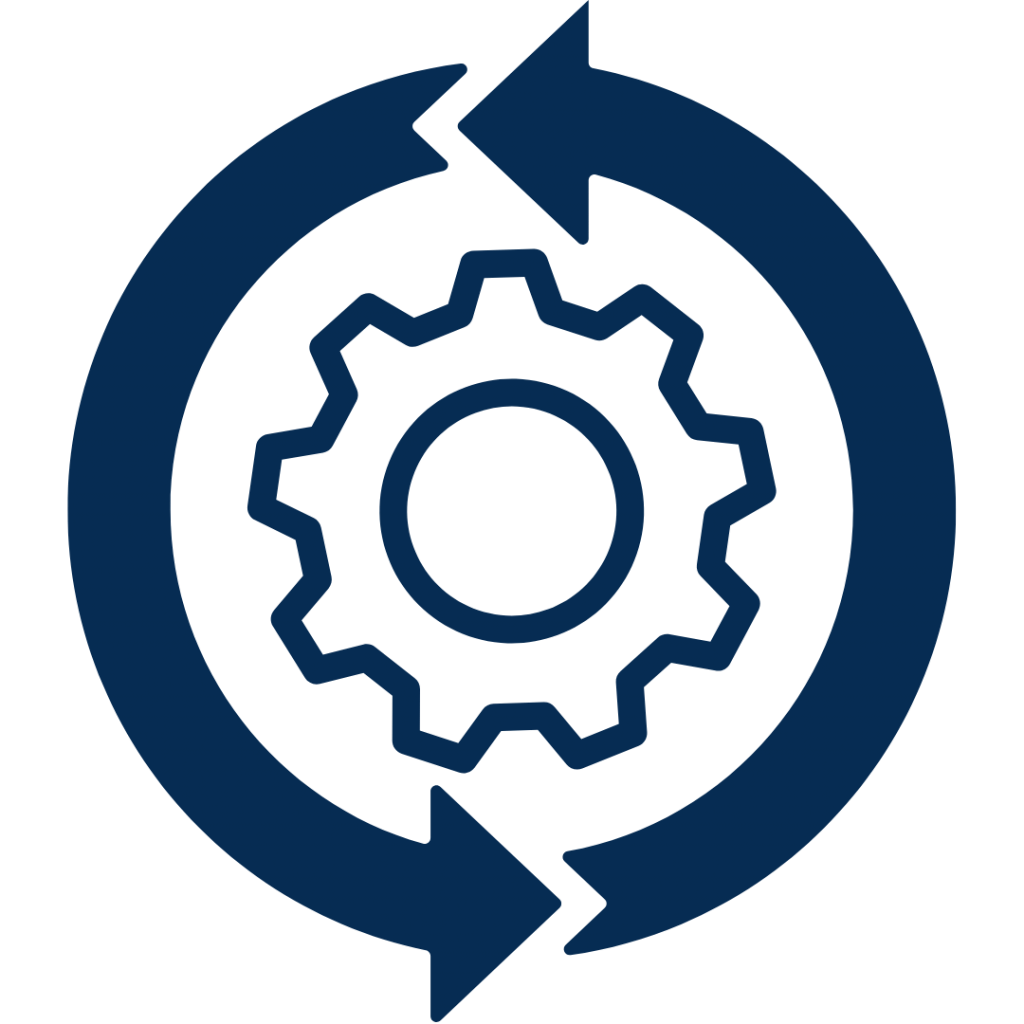
Process Automation
With ultimate goals toward enhancing productivity, improving product quality, ensuring regulatory compliance, and reducing operational costs, Huffman Engineering has their eyes on the complete process from start to finish.
Our customized automation systems can be integrated with other enterprise systems like Manufacturing Execution Systems (MES) and Enterprise Resource Planning (ERP) to streamline operations, improve data flow, and facilitate better decision-making. By analyzing data collected during manufacturing, our automated systems can help equip your teams in identifying inefficiencies and suggesting improvements leading to a reduction in production costs, increased throughput, and enhanced product quality.
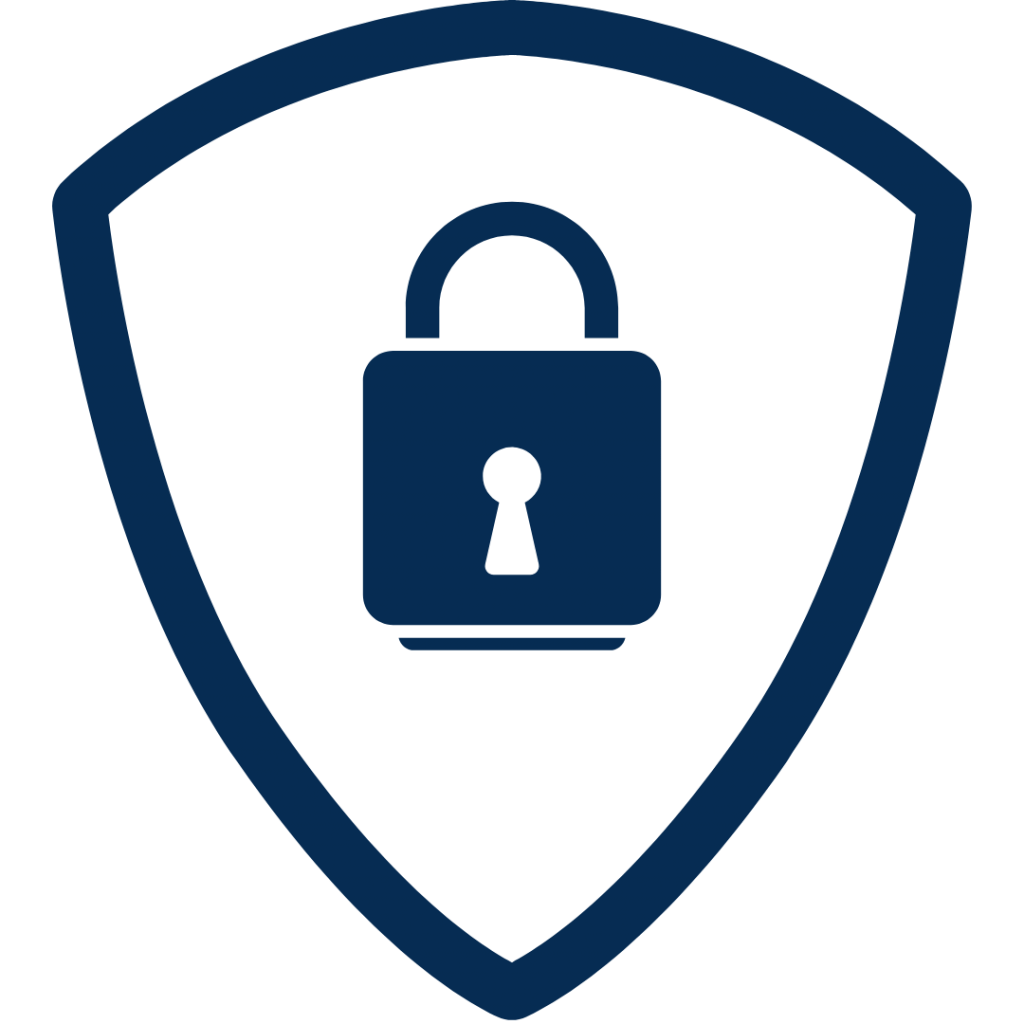
Networking & Security
Networking and Security are critical components of control automation systems in manufacturing due to the industry’s stringent requirements for reliability, data integrity, and regulatory compliance. Our focus has always been enabling real-time monitoring and control of manufacturing processes from centralized locations. That way, operators and engineers can access live data, make adjustments remotely, and quickly respond to any issues that arise.
Our effective networking and security practices in control automation systems enhance operational efficiency, data integrity, compliance, and overall system reliability. They help manufacturers meet regulatory requirements, protect intellectual property, and ensure the consistent quality of their products.
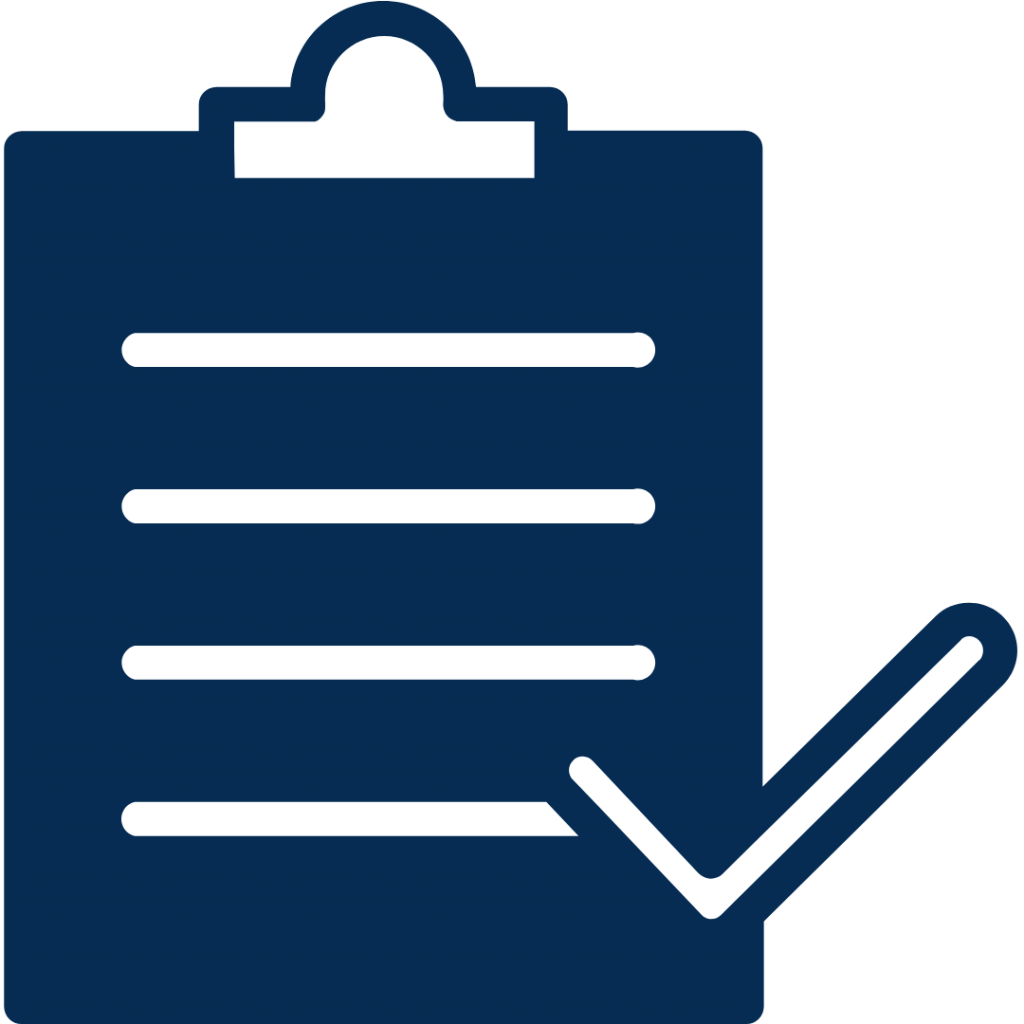
Reporting For Compliance
Reporting and compliance in the manufacturing industry are essential for maintaining regulatory standards, ensuring public health, and promoting environmental protection. Effective reporting and compliance practices offer several benefits to plant manufacturers, regulatory agencies, and the communities they serve.
We pride ourselves on striving to make the communities we live and work in safer for everyone and that includes regulatory compliance, improved operational efficiencies, community transparency, data management and security precautions.
Huffman Engineering, Inc. Featured on Control System Integration Webinar
Huffman Engineering Inc. (HEI) joined Applied Manufacturing in presenting a webinar on Control System Integration: Automation Success in Action https://www.controleng.com/webcasts/automation-series-control-system-integration-advances-competitiveness/ The presentation “How to Automate Series: Control System Integration Advances […]
The Legacy Equipment Challenge at a Pharmaceutical Manufacturer
Searching eBay to replace old parts for your legacy equipment? This article details how one customer successfully addressed this challenge. In the world of pharmaceutical manufacturing, downtime can be a […]
Process Automation
Material Handling
Packaging & Palletizing
Lab Systems
Designing and implementing systems that automate repetitive or complex processes to improve efficiency, consistency, and accuracy is what we do well. We pride ourselves on collaborating with clients to understand their specific needs and objectives for automation. This includes identifying the processes to be automated and any particular goals such as reducing manual labor, increasing throughput, or improving data accuracy. Through systematic process analysis, we analyze the existing processes to be automated, map out workflows, identify bottlenecks, and determine key performance indicators (KPIs) for success.
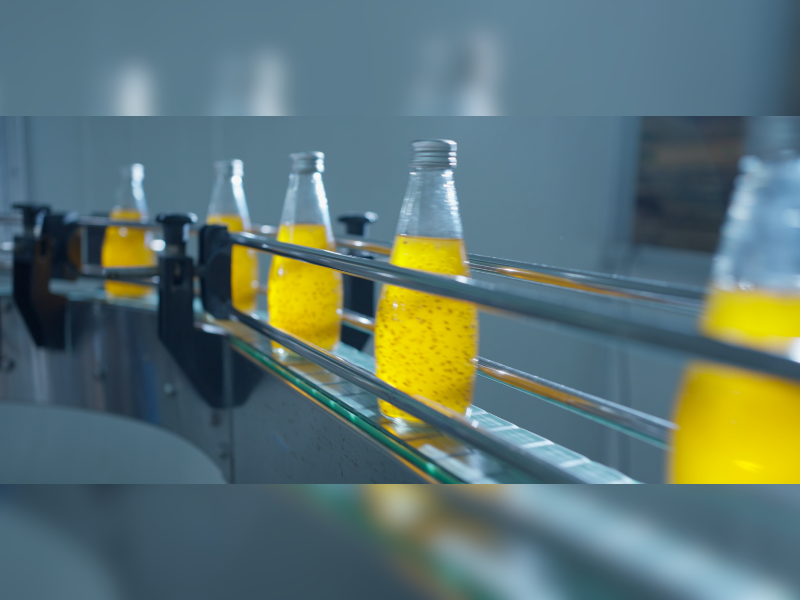
System Design & Architecture
Automation Strategy: Develop a strategy that aligns with the client’s goals. Decide on the level of automation required, from simple task automation to complex process automation involving multiple systems.
Component Selection: Choose appropriate automation technologies, such as:
- Robotic Process Automation (RPA): For automating repetitive tasks typically done by humans.
- Industrial Automation: For manufacturing processes, including PLCs (Programmable Logic Controllers) and SCADA systems.
- Business Process Management (BPM) Systems: For orchestrating workflows and integrating different business processes.
- Custom Software Development: For unique or complex automation needs that require tailored solutions.
Integration Planning
System Integration: Plan how the automation system will interface with existing systems and software. This includes data integration, API connections, and middleware solutions.
Data Management: Ensure proper data flow and consistency across systems. Design data transformation, storage, and retrieval processes to support automation.
Development and Configuration
Automation Script Development: For RPA, develop scripts or bots that execute the automated tasks. This involves scripting the steps that the bots will perform and handling exceptions and errors.
System Configuration: Configure automation tools and platforms according to the design specifications. This includes setting up workflows, defining rules, and establishing triggers.
Custom Development: If needed, develop custom software components or modifications to existing systems to facilitate automation.
Effective material handling through system integration brings substantial benefits in terms of efficiency, accuracy, safety, cost savings, space utilization, inventory management, flexibility, quality control, customer service, and data-driven insights. By leveraging integrated systems, businesses can achieve more streamlined and effective material handling operations, leading to improved overall performance and competitive advantage. This is one thing Huffman Engineering has found over our decades of experience with clients in the manufacturing and material handling industries.
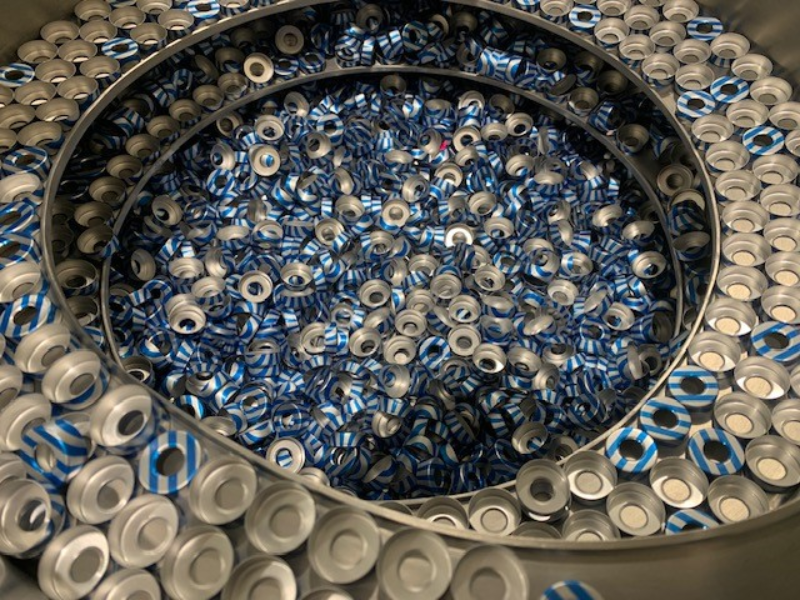
Increased Efficiency: We streamline operations, integrating material handling systems with other operational systems (like inventory management, production scheduling, and logistics) ensuring a seamless flow of materials. This minimizes delays and interruptions, leading to smoother operations. Our automated processes reduce the need for manual handling, which speeds up material movement and processing. Systems like conveyor belts, vision systems and robotic pickers can handle large volumes of materials quickly and accurately.
Improved Accuracy: Automated material handling systems reduce human errors associated with manual handling, such as misplacement, incorrect picking, or counting errors. Integration with inventory systems ensures accurate tracking and management of materials and integrated systems provide real-time data on material status, location, and inventory levels. This helps in maintaining accurate records and making informed decisions.
Enhanced Safety: Automated systems minimize the need for manual lifting and carrying, which reduces the risk of workplace injuries. This contributes to a safer working environment. Integrated safety features, such as sensors and automated stop functions, help prevent accidents and equipment malfunctions.
At Huffman Engineering we know that effective packaging through system integration delivers numerous benefits, including increased efficiency, improved accuracy, cost savings, flexibility, better inventory management, enhanced safety, and compliance. Additionally, it improves customer experience, provides valuable data-driven insights, supports sustainability efforts, and enhances operational reliability. By leveraging integrated packaging systems, businesses can achieve more efficient, accurate, and cost-effective packaging processes, ultimately leading to better performance and competitive advantage.
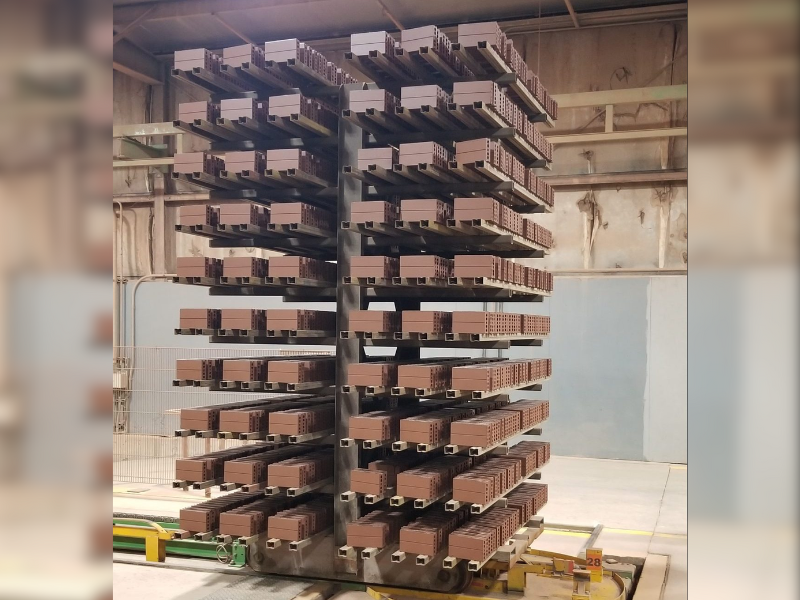
Enhanced Customer Experience: Integration with labeling systems ensures that products are labeled correctly with accurate information, enhancing customer satisfaction and reducing the likelihood of returns due to labeling errors. Reliable packaging processes ensure that products reach customers in good condition, maintaining quality and enhancing the overall customer experience.
Data-Driven Insights: Integrated systems provide valuable data on packaging performance, including throughput rates, error rates, and machine utilization. This data can be analyzed to identify areas for improvement and optimize processes. Trend analysis and data collected from integrated systems can reveal patterns, helping businesses make informed decisions about packaging strategies and process improvements.
Operational Reliability: Automated and integrated systems reduce the frequency of breakdowns and maintenance needs, leading to higher operational reliability and less unplanned downtime. Integration with maintenance management systems allows for predictive maintenance, where data from packaging equipment is used to anticipate and address issues before they lead to failures.
Laboratory (Lab) system project management expertise from start to finish qualifying, integrating, validating new and/or upgrading existing lab systems ensuring regulatory compliance are well within Huffman Engineering, Inc.’s (HEI) experience. HEI experienced resources can complete contractor training, clean zone gowning training, and can be provided with facility access to the lab systems environment.
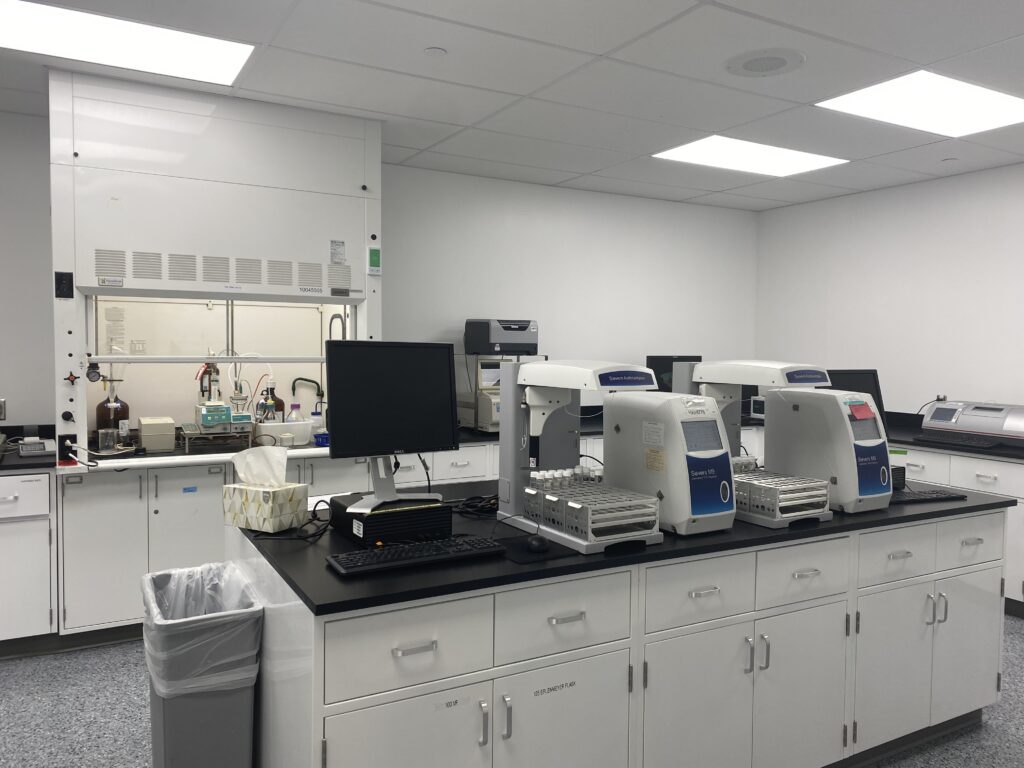
Laboratory systems specification design, networking & security
Authorship & facilitation of qualification and validation documents, Validation Plan (VP), User Requirement Specification (URS), Installation Qualification (IQ), Operational Qualification (OQ), and Performance Qualification (PQ)to meet complex regulatory compliance
Design of server & workstation builds to meet/exceed lab system requirements, including operating systems (OS), hardware, software and other system components
Implementation & configuration of domain security groups on servers & network file share data storage locations
Laboratory system software installation & configuration
Implementation & configuration of an automated data back-up & maintenance strategy
Configuration of user access for security and audit logs
Have Questions? Like to Request a Quote? Contact Us Below.
Toby Varner, PMP
Industrials Manager
Did you know?
Toby is an avid hunter.
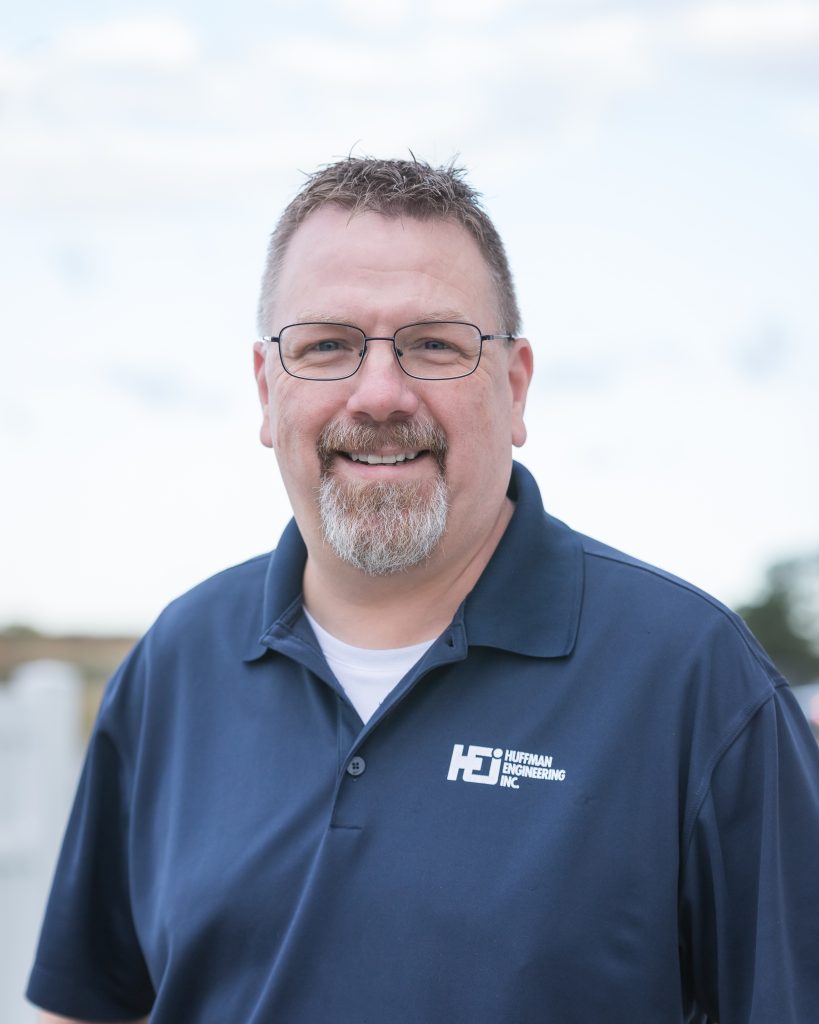