Cutting Edge Pharmaceuticals & Life Sciences
Your Health. Our Priority.
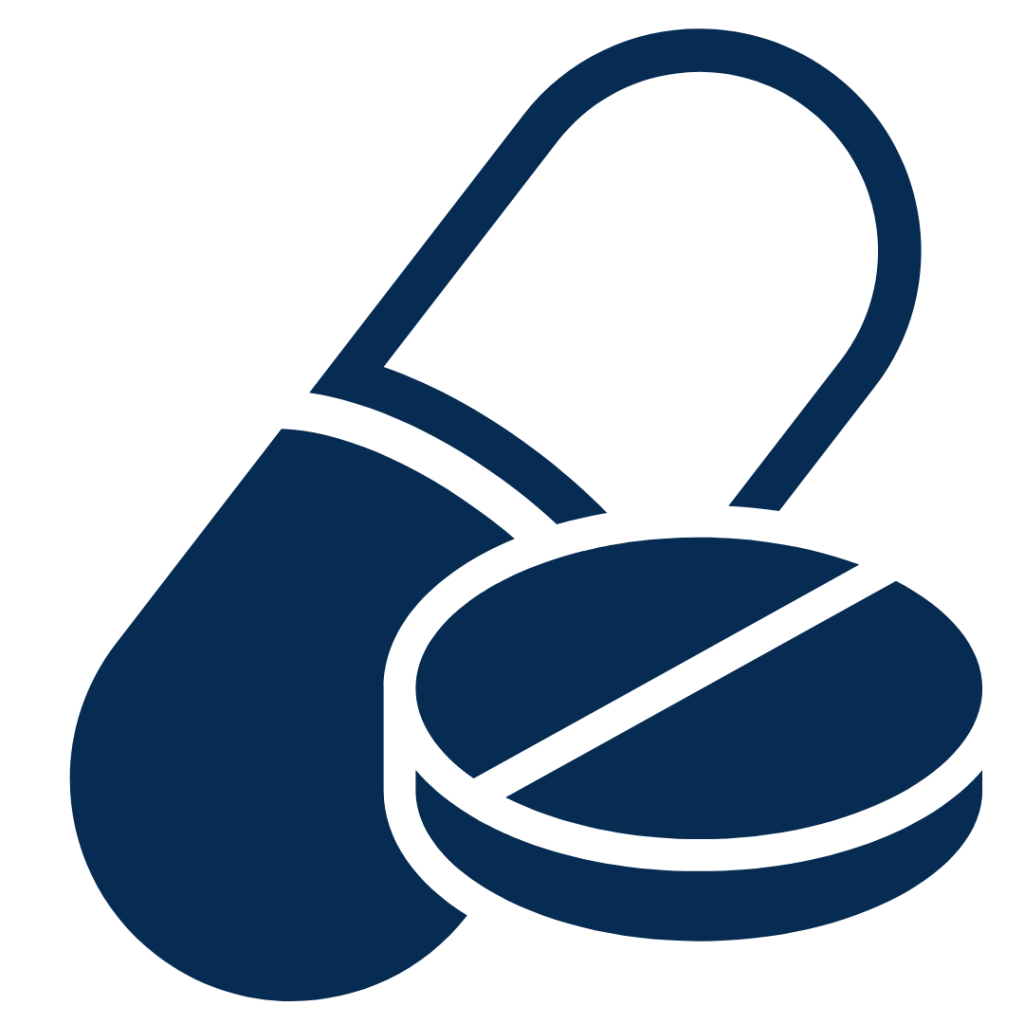
Process Automation
With ultimate goals toward enhancing productivity, improving product quality, ensuring regulatory compliance, and reducing operational costs, Huffman Engineering has their eyes on the complete process from start to finish.
Our customized automation systems can be integrated with other enterprise systems like Manufacturing Execution Systems (MES) and Enterprise Resource Planning (ERP) to streamline operations, improve data flow, and facilitate better decision-making. By analyzing data collected during manufacturing, our automated systems can help equip your teams in identifying inefficiencies and suggesting improvements leading to a reduction in production costs, increased throughput, and enhanced product quality.
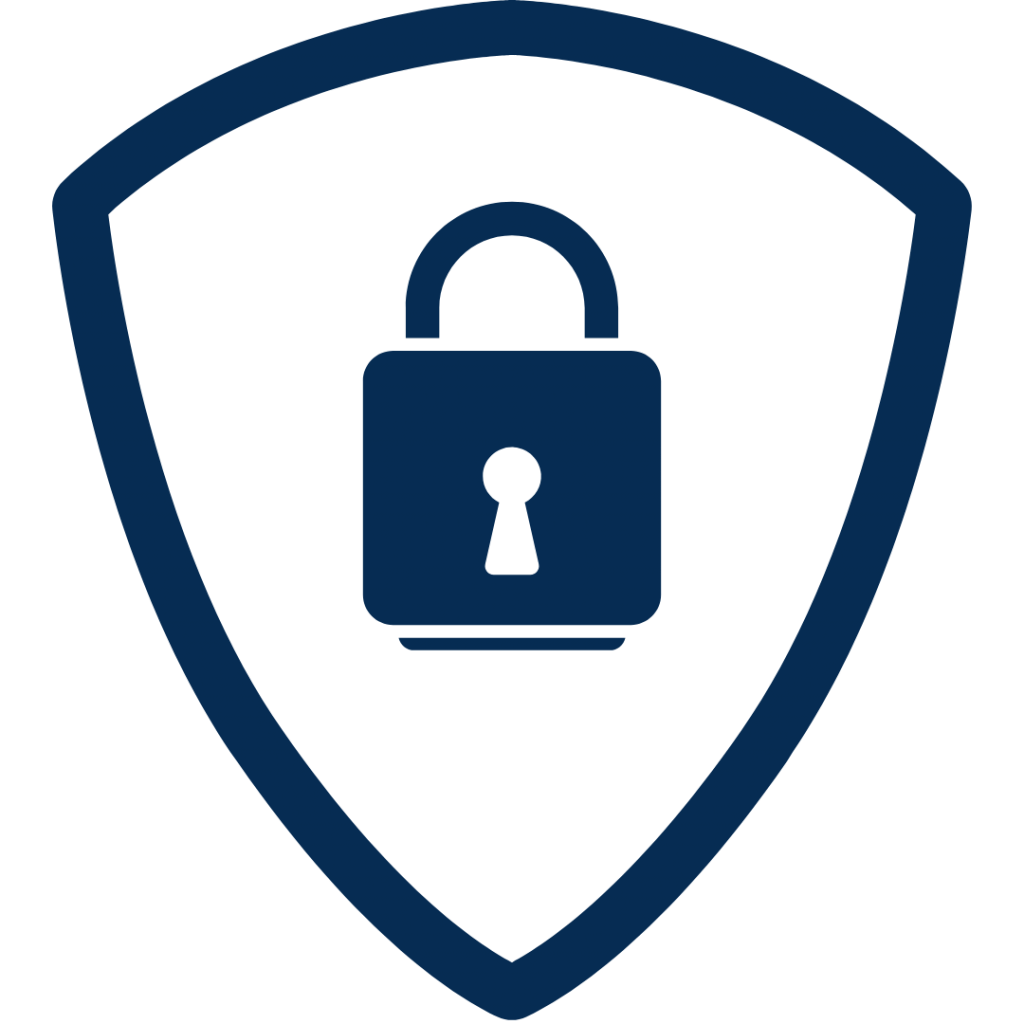
Networking & Security
Networking and Security are critical components of control automation systems in pharmaceutical manufacturing due to the industry’s stringent requirements for reliability, data integrity, and regulatory compliance. Our focus has always been enabling real-time monitoring and control of manufacturing processes from centralized locations. That way, operators and engineers can access live data, make adjustments remotely, and quickly respond to any issues that arise.
Our effective networking and security practices in control automation systems enhance operational efficiency, data integrity, compliance, and overall system reliability. They help pharmaceutical manufacturers meet regulatory requirements, protect intellectual property, and ensure the consistent quality of their products.
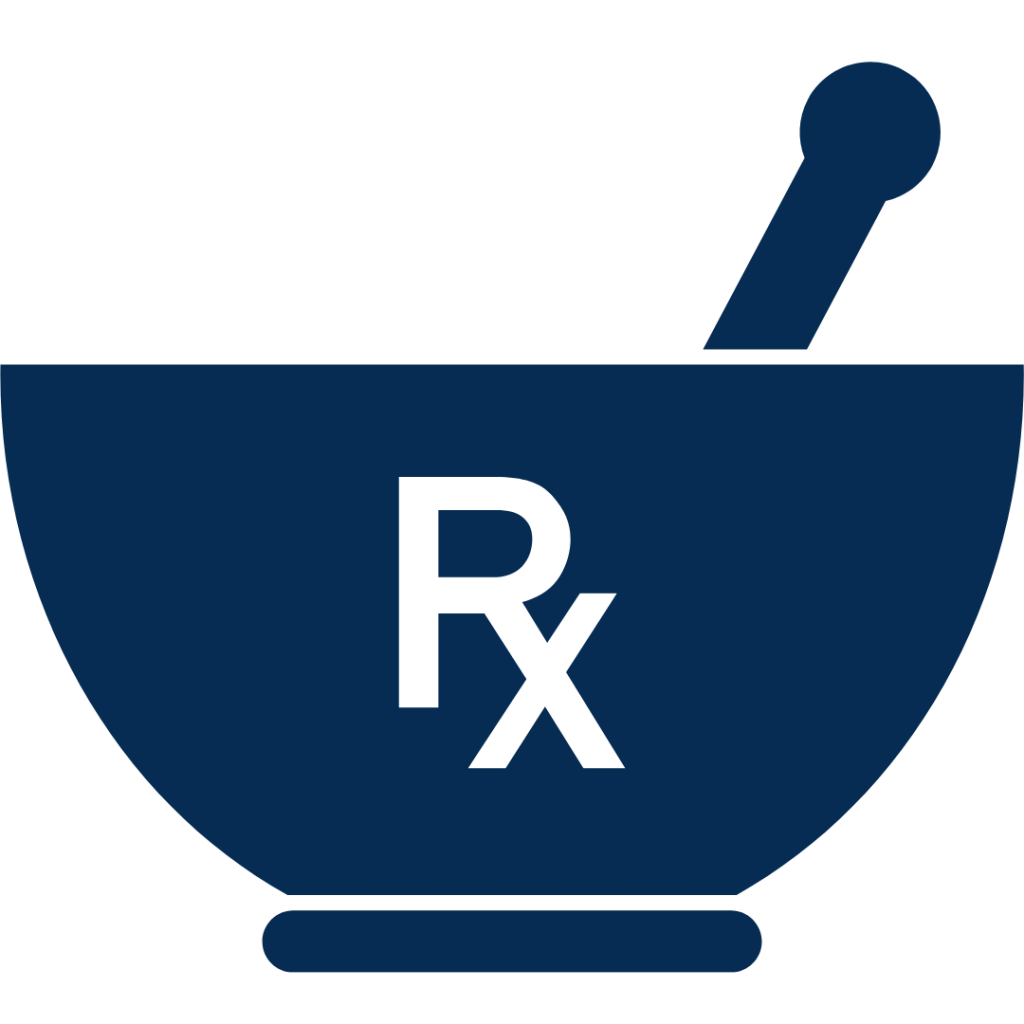
Commissioning, Qualification & Validation
Confirming system integrity and operational efficiency in our customized systems so they are working well for you is what we pride ourselves on. But we go above and beyond the commissioning stage to also offer qualification and validation services either alongside your internal teams or as a standalone service while we design, build and complete projects.
Our expertise in Installation Qualification (IQ), Operational Qualification (OQ), and Performance Qualification (PQ) exceeds many of our competitors just based on our years of experience in the pharmaceutical and life sciences world. As qualification and validation regulations change, keeping up to date with institutions like the FDA becomes a complex position so having a skilled integrator by your side to help you navigate the ever-changing world can save you time and money.
Alarming Truth of Upgrades
GLOBAL Animal Health – SmartSights (WIN-911) Upgrades A global Animal health pharmaceutical plant upgraded their…
AI-based Vision Inspection Systems Make More Informed Decisions
Mechanical Engineer Sean Dugan shares a “vision” for AI and vision systems in Food Engineering magazine……
Single-Use Technologies
Consumer & Animal Health
Batch
Lab Systems
Single-use technology in pharmaceutical manufacturing offers substantial benefits, including reduced risk of contamination, lower cleaning and validation costs, increased flexibility, faster turnaround times, and improved process efficiency. These advantages contribute to more efficient, cost-effective, and reliable production processes, which are essential for maintaining high-quality standards and meeting regulatory requirements. HEI’s expertise in implementing single-use technology and designing full single-use systems is a benefit to all pharmaceutical companies looking to upgrade or those who are actively utilizing this technology.
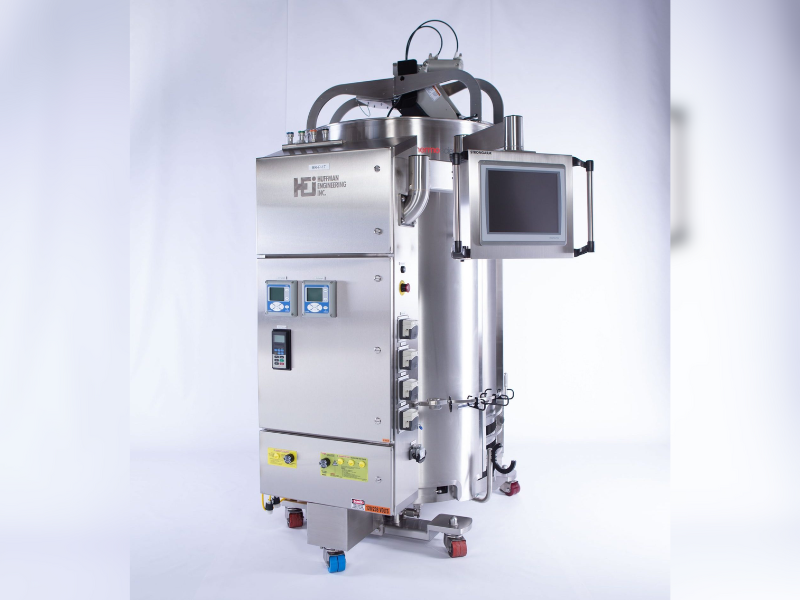
Improved Process Efficiency: Single-use systems are designed for optimal performance with minimal downtime. They often come with integrated features that enhance process efficiency, such as pre-assembled connections and streamlined workflows.
Enhanced Quality Control: The use of disposable components helps maintain consistent quality by reducing the variability associated with cleaning and reusing equipment. Each batch starts with brand-new, sterile components, which helps ensure uniformity in production.
Lower Cleaning and Validation Costs: Single-use components do not require cleaning or sterilization between uses, which reduces the time and cost associated with cleaning validation. This can lead to significant savings in both labor and operational expenses.
Systems integrators with experience in both consumer and animal health offer a range of benefits that enhance the efficiency, quality, and compliance of pharmaceutical manufacturing processes. Their expertise in these diverse sectors allows them to bring valuable insights and solutions that address the unique challenges and requirements of each industry. This comprehensive industry knowledge allows our engineers to design systems benefiting from the best practices across industries.
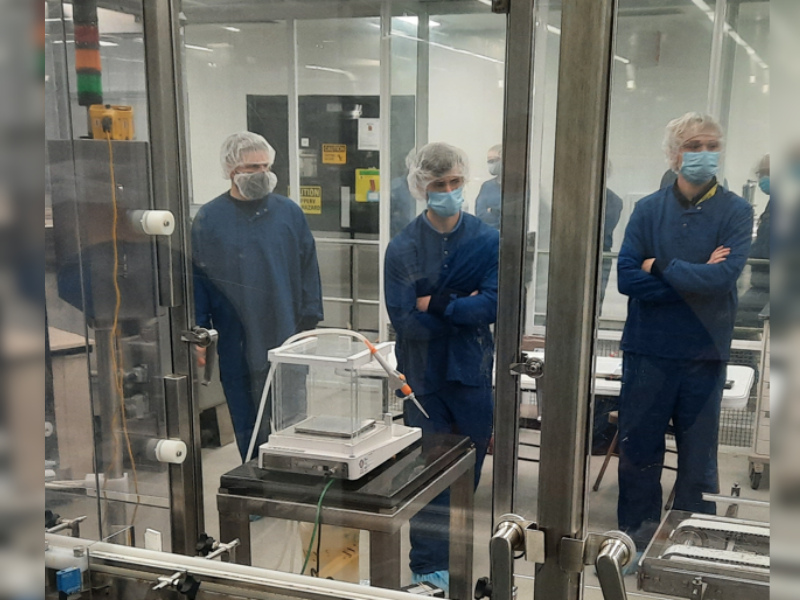
Enhanced Regulatory Compliance: These integrators are well-versed in the regulatory frameworks governing both consumer and animal health products, such as FDA and EMA guidelines. Their expertise ensures that the systems they design and integrate comply with all relevant regulations, reducing the risk of non-compliance and facilitating smoother regulatory submissions and inspections.
Faster Time-to-Market: By leveraging their experience and expertise, systems integrators can accelerate the design, implementation, and optimization of manufacturing systems. This leads to faster time-to-market for new products, allowing companies to respond quickly to market demands and opportunities.
Effective Problem Solving: Exposure to the challenges and solutions in both consumer and animal health sectors enhances an integrator’s problem-solving capabilities. They are adept at addressing complex issues that may arise during manufacturing, ensuring smooth and efficient production processes.
Huffman Engineering’s role and experience in batch manufacturing plays a critical role in quality control, regulatory compliance, and ensuring the consistency and safety of pharmaceutical products.
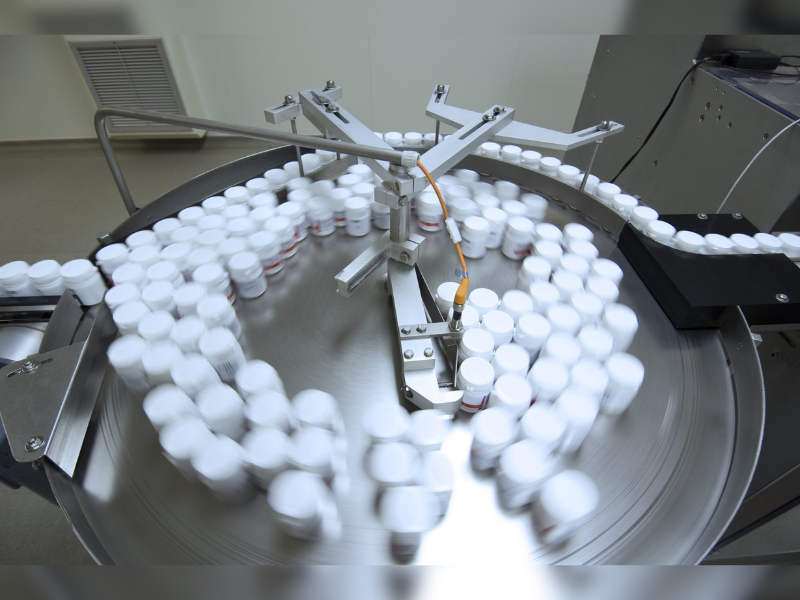
Quality Control: Each batch undergoes testing to ensure it meets predefined specifications and quality standards. This includes testing raw materials, in-process samples, and final products.
Consistency: By producing products in batches, manufacturers can control and maintain consistency across products. Consistency is vital for ensuring that each unit of the product performs as intended.
Traceability: Batch numbers provide a way to trace back to specific production runs, raw material sources, and processing conditions. This traceability is essential for investigating quality issues and ensuring accountability.
Laboratory (Lab) system project management expertise from start to finish qualifying, integrating, validating new and/or upgrading existing lab systems ensuring regulatory compliance are well within Huffman Engineering, Inc.’s (HEI) experience. HEI experienced resources can complete contractor training, clean zone gowning training, and can be provided with facility access to the lab systems environment.
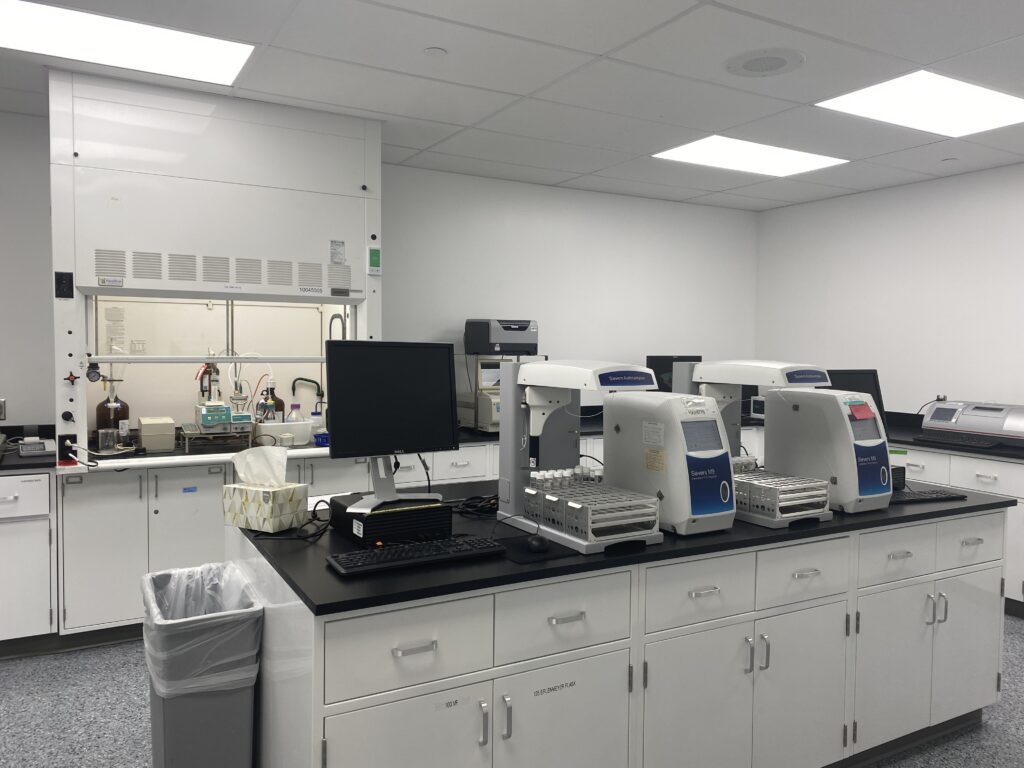
Laboratory systems specification design, networking & security
Authorship & facilitation of qualification and validation documents, Validation Plan (VP), User
Requirement Specification (URS), Installation Qualification (IQ), Operational Qualification (OQ), and
Performance Qualification (PQ)to meet complex regulatory compliance
Design of server & workstation builds to meet/exceed lab system requirements, including operating
systems (OS), hardware, software and other system components
Implementation & configuration of domain security groups on servers & network file share data storage
locations
Laboratory system software installation & configuration
Implementation & configuration of an automated data back-up & maintenance strategy
Configuration of user access for security and audit logs
Have Questions? Like to Request a Quote? Contact Us Below.
Toby Varner, PMP
Business Development
Did you know?
Toby is originally from Lincoln, NE.
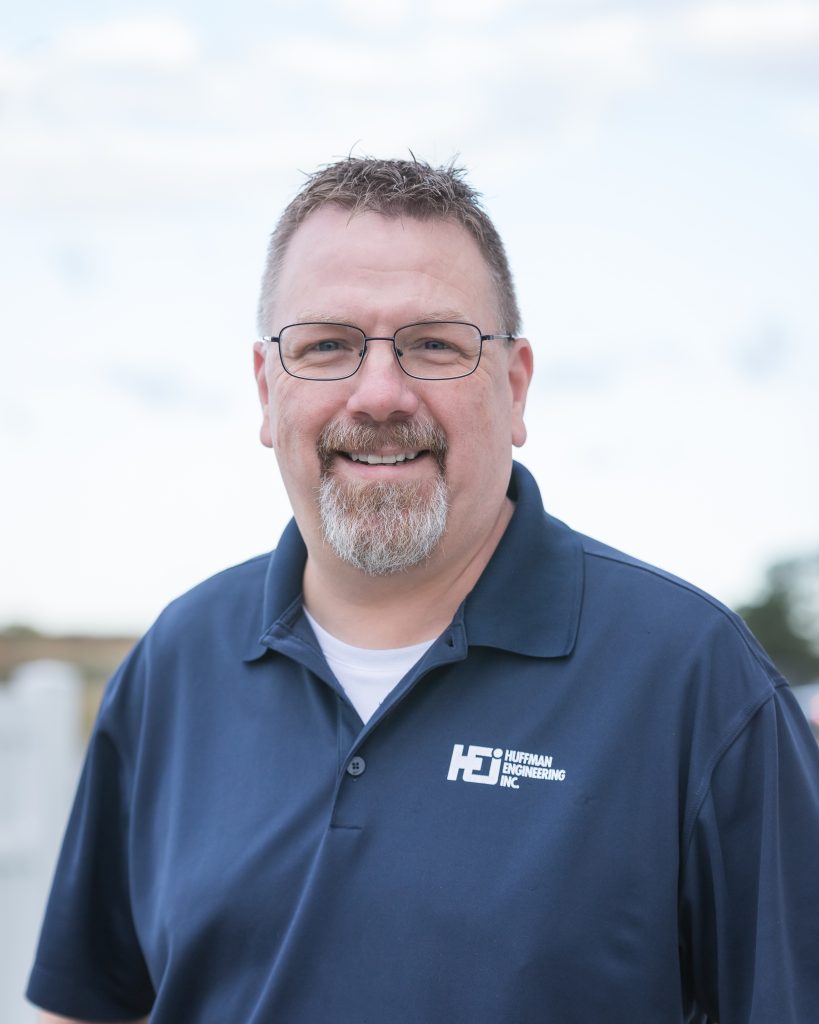